A step ahead in the recovery of edge trims
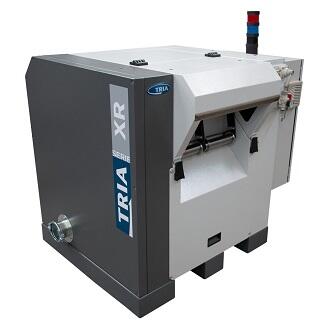
Increasingly faster extrusion lines, thinner materials and PS, PP, PLA, PET with slippery and sticky additives: these are some of the factors that make grinding process of trims more difficult. Based on careful studies, perfect design and tests at customer companies, Tria from Cologno Monzese (near Milan), has brought to life the new generation of grinders for edge trims, the XR series, on display at the K 2019 show.
In addition to the main characteristics that distinguishes Tria machines such as the discharge surface equal to 50% of blades rotation length and the access without tools to the main parts subject to ordinary maintenance, the XR grinders incorporate the following innovations:
- grinding of edge trims with slippery and sticky additives, from thickness of 100 micron;
- speed regulation from 0 to 156 m/min against 110 m/min of the previous TRK version:
- possibility to set to zero the haul-off speed with active accumulator, avoid slipping of rollers and breaking of material during the change of the reel; also material windings are minimized;
- standard: possibility of synchronizing the haul-off speed with production line;
- new design with moving parts inside the perimeter in order to work in total safety;
- noise reduced by 4dB compared to the previous TRK series;
- remote control via a Bluetooth application;
- ease of use and maintenance without tilting of the haul-off;
- two series: one with double haul-off (190 mm), one with single haul-off (320 mm) for throughput rates up to 250 kg/h.
Lastly the new grinders stands out for their flexibility. One motorized roller and one free roller: possibility to add an optional kit with the second motorized roller, in case of new material formulations.
At K 2019, Tria will be also exhibiting its Smart Grinder range of applications incorporating Industry 4.0 features and technology and adopting Euromap directives in terms of communication protocols OPC-UA between different machines, has created applications that can be easily adaptive to the customers production line in different manufacturing environments.
The new applications offer all-round continuous monitoring of the production system, consumption levels, blades wear, temperature during material feeding (thus avoiding dust, angel hair and overheating of material inside grinding chamber) as well as system diagnostic, remote line control and remote assistance.
On top of all this, Industry 4.0 also stands for sustainability and energy efficiency, as only 5% of installed power is used for dry operation and only 30% for grinding. Finally,
energy consumption is minimized thanks to a default function which effects sequential automatic shutdown in case of prolonged absence of material at the entrance of the grinder.