Co-extruded TPEs with optimum adhesion to PA for high-quality corrugated tubes
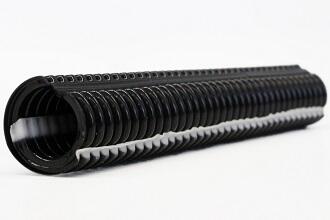
An innovative new thermoplastic elastomer (TPE) family made by Kraiburg TPE transfers the established properties of injection-mouldable TPEs for multicomponent applications with polyamide to extrusion. Cable management systems in motor vehicles are the first application for which the Schlemmer Group (Munich) is producing new types of Polyflex corrugated tubes by co-extruding PA and a Thermolast K AD/PA/CS2 compound.
Direct adhesion of TPEs to polar plastics, such as PA, requires carefully selecting the two components and matching them to the specific requirements for each application and processing method. Kraiburg TPE has performed an extensive study of these criteria and is supporting its customers in using PA/TPE applications by providing specific recommendations and custom-engineered compounds. Established multicomponent applications of this type include injection-moulded gaskets, mounting elements, cable bushings and membranes.
The new types of Polyflex corrugated tubes for flexible cable management systems, particularly in vehicle construction, mean that the Schlemmer Group’s requirements for TPE components have risen. In order to avoid sharp edges and allow faster installation thanks to slit corrugated tubes, the product developers’ design was aimed at combining PA and TPE by co-extrusion.
“We were looking for a TPE that not only provides the necessary heat resistance and cold toughness for use in motor vehicles, but can also be extruded economically - i.e. without the use of bonding agents - with polyamide. It was also necessary to ensure reliable adhesive strength in this material composite. Thermolast K AD/PA/CS2 is a compound that we found among Kraiburg TPE’s Thermolast K materials that provides this combination of properties”, explains Michaela Zagler, Material Development Specialist at the Schlemmer Group.
After extensive testing, Schlemmer chose a TPE from the new AD/PA/CS2 Thermolast K series, which was specially developed for sophisticated injection moulding and co-extrusion applications with polyamides such as PA6, PA6.6 and PA12. The products are characterized by their excellent adhesiveness and provide an outstanding compression set. While their maximum service temperature is 125°C (3,000 hours), they also resist peak temperatures of up to 150°C for short periods (240 hours). They also feature high elongation at break, tear strength and resistance to tear propagation, as well as slow burning (UL94 HB). In addition, the TPE family provides a very aesthetic surface quality with excellent wear resistance that does not require finishing, at a hardness range between 40 and 80 Shore A. The selected compound shows a peeling resistance of more than 8.5N/mm during tests in accordance with the VDI 2019 standard.
Thermolast K compounds in the AD/PA/CS2 series are available worldwide in natural colour (colourable) as well as in black, and they are produced in accordance with identical quality standards at all Kraiburg TPE sites.