A processing technology in good health
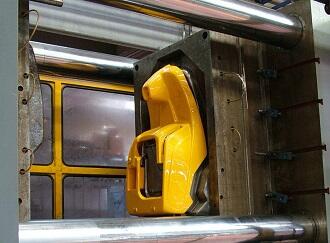
Injection moulding is the most important processing method for mass production of plastic parts. Worldwide, almost 55 million tons of plastics are liquefied every year, then injected into various moulds, and after cooling removed as a finished product. From small Lego bricks to large pipe fittings, almost everything is possible; the flexibility of size and form of this method expanded possibilities of plastic design enormously. Injection moulding enables the substitution of traditional materials due to the low weight and the freedom of design.
According to the market research company Ceresana, in 2015 about 54% of the plastics used for injection moulding were used in the region Asia-Pacific. North America and Western Europe followed with market shares of 15.4% and 14.3%. The most important sales market for injection moulded products is the packaging industry, which mainly protects food with containers, cans, mugs, bowls, boxes, and closures of any kind. Packaging made of plastics offers numerous advantages over other materials. Besides their low weight and a reduced fracture susceptibility, plastic packaging can profit in some segments from its transparency or resistance against chemicals.
The second largest - and fastest growing - sales market is the transportation industry which, for example, uses injection moulding for dashboards, bumpers, and headlights. Analysts of Ceresana expect global demand in this application area to increase by 3.7% per year in the period 2015-2023.
Different kinds of plastics are used for the various application areas. For example, almost 70% of all packaging but only 12% of all construction products are made of polypropylene. Overall, polypropylene is the most important type of plastics for injection moulding. Over the past eight years, global demand rose by an average of 3.8% per year. The second most important plastic type for injection moulding is polyethylene with a market share of 20%.