Gefran Supplier Day under the banner of sustainability: reducing carbon footprint by 25% by 2030
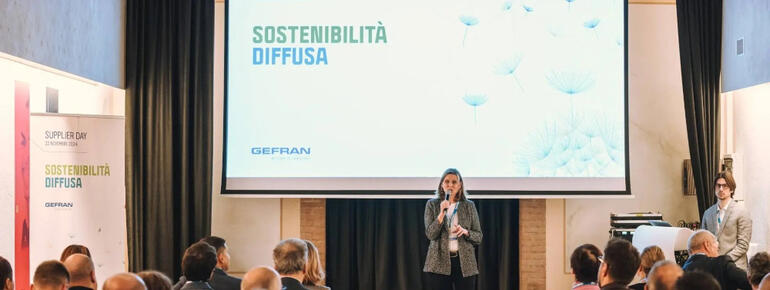
The fourth edition of the Supplier Day involved the Gefran’s main suppliers who, through concrete projects on specific areas, are contributing to Gefran's decarbonization process. Gefran organized the 2024 Supplier Day, an annual workshop where the Italian multinational company meets with key representatives of the local supply chain to share values, goals and action plans, spreading a common culture of sustainability. The sustainable supply chain represents specifically one of the pillars of Gefran's strategic plan for sustainability.
Once again for 2024, Supplier Day confirms itself as an eagerly awaited event for Gefran's supply chain players, which consolidated the commitment to sustainability of the many participants, generating many concrete results: a project that involved the company's main suppliers, the launch of new initiatives in the ESG sphere and offered support to small businesses in the area. Active participation made it possible to achieve the goal of fostering a shared culture of sustainability, creating value for all those involved, allowing for the development of new opportunities and initiatives, and bringing the company closer to the goals of the strategic sustainability plan. The event provided an opportunity to align each other on the projects that the company's suppliers have implemented over the past 12 months to reduce their Scope 1 and 2 emissions, contributing to Gefran's goal of decreasing its carbon footprint impact by 25% by 2030.

“Sustainability has always guided Gefran’s development. As it is one of the main strategic elements that allowed the group to steadily grow and gain stability and will keep sharing the direction where to aim”, confirmed Giovanna Franceschetti, Vice Chairwoman of Gefran, with delegation to the sustainability. “Along this path, the concrete actions of our suppliers are of ever-growing importance to reach a sustainable growth for all of us”.
Specifically, Gefran invited its suppliers to identify and promote concrete, joint actions during the year aimed at reducing the emissions produced. These projects could cover five areas: the use of self-produced energy or energy derived from renewable sources, the efficiency of production facilities, the optimization of logistics, the use of low-impact packaging, and other specific initiatives. Most of the companies in the area that make up the company's supply chain joined this call, implementing 30 projects related to the various areas of action identified by the Group in its call to action.

“I’m very proud of our suppliers effort towards the reduction of their carbon footprint, that marks how our commitment to sharing a common sustainability culture is producing important results”, stated Stefano Mazzola, Chief Procurement Officer in Gefran. “In Gefran’s path towards decarbonization, the supply chain’s role is quite relevant, considering it can offer a decisive contribution to reach our sustainability goals, and, the 2024 Supplier Day has confirmed how well we are working”.
The 2024 Supplier Day was therefore an opportunity to showcase the projects and efforts made by Gefran's suppliers in their journey toward reducing their carbon footprint: participants debated the spread of sustainability and initiatives to be implemented in the near future, sharing experiences, successes and difficulties. In addition, three particularly significant projects implemented by three companies in the value chain were presented.
The first, concerns a plan to reduce the carbon footprint by using energy from renewable sources and decreasing energy consumption, through the replacement of lighting systems, hot air generators, and the development of a production process efficiency methodology. The second, allowed us to map the carbon footprint of the components used by Gefran, starting from the supplier's production facilities to delivery. This made it possible to define a plan to reallocate production to plants with lower environmental impact. The project also incorporates a review of how products are transported in order to further reduce the overall environmental impact. The third involved the development of a travel management app: thanks to an algorithm, it optimizes routes by assigning employees to companies closest to their domiciles and, when possible, suggests carpool combinations to reduce costs and environmental impact.