Hybrid systems for continuous assembly
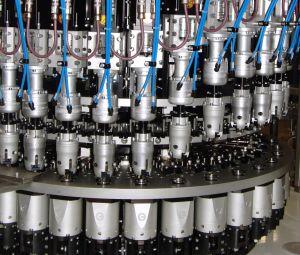
Technological innovations. Experimental applications. Study of new solutions, designed to provide immediate and effective responses even when faced with the most complex needs of the market. Through these values, Gefit, a worldwide player in the manufacturing of moulds for thermoplastics and high-speed assembly systems, has given new impetus to the study and design of the “hybrid machines”. The goal is as simple as it is important: to cross new frontiers, moving from traditional mechanical solutions to modern and efficient electric motors, with obvious multiple benefits. A Gefit hybrid machine can carry out the continuous assembly of components, which, previously, had to be assembled by using different systems (index or step-by-step). The traditional closures applied on food cartons, for example, are now realized by using the hybrid technology. Another key issue, addressing this topic, regards the possibility to realize the screwing operation of the product only after performing a particular angular search, so as to overcome the critical points of traditional fastening, such as the annoying crash on threads. Moreover, a sort of "gentle screwing" is now possible, with a substantial reduction in the amount of dust produced by friction between the elements. Furthermore, the hybrid machine is able to perform linear pressfits controlling the coupling force between the elements in several points, with obvious benefits in terms of waste. An additional check beyond the traditional visual inspection. Not to mention that the use of brushless motors on these machines also allows to obtain a firm grip on the workpiece with the upper spindle completely stopped: a very important detail, which reduces, almost to zero, the risk of damaging the component. In brief, starting from a single angular position, orientation and pressfit can be performed, combining linear and rotary motion. And what’s more, in continuous.