Two more CBF for the Chinese dairy
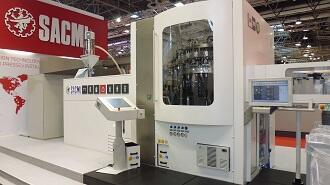
Major Chinese company in the dairy sector purchases two more CBF (Compression Blow Forming) systems, taking the total number of installed solutions to four. Highly innovative process combining high bottle quality with weight reduction proved to be a major plus factor.
These, then, are the distinctive characteristics of the CBF technology by Sacmi, which has now won over a leading firm on the Chinese dairy market, a company that’s already one of the world's top ten players in the industry. This latest order doubles the existing number of machines, taking the total number of currently installed CBF machines to four and making this customer one of the world's biggest users of Sacmi technology.
Thanks largely to Sacmi's ability to transfer the intrinsic advantages of compression technology to another industry - plastic container production using the different commercially available resins - the CBF platform aroused the interest of this key dairy player following the outcome of in-depth comparative analysis with extrusion blow-moulding (EBM), still widely used for pasteurized product packaging.
So what are the competitive advantages of CBF? A cycle time of 7 seconds and, simultaneously, a container weight that - against an increase in quality - drops from 19 to about 15.5 grams.
Designed to produce 200-ml HDPE containers, these CBF machines provide a weight reduction of about 20% - with related energy and raw material savings - and a consequent increase in competitiveness. This goes hand in hand with the high consistency and repeatability of the highly innovative CBF process, based on continuous extrusion of the plastic, which is then cut into doses of pre-determined size. The latter are then inserted in an open mould and compressed to make a preform. The result: a single technological platform that allows containers to be made directly from the pellet.
A top-flight company, the customer does business with firms all over the world and works with major US research bodies. This, then, is a strategic order for Sacmi, essential to reinforcement of its international position on the dairy market and, in parallel, development of further orders, not just with this technology but also other group-supplied beverage solutions such as CCM compression presses for the manufacture of plastic caps and the new modular labellers.
The customer's investment decision was determined not just by the anticipated boost in productivity and the lower container weight, but also by the possibility of achieving, via this technology, maximum process repeatability and a general increase in container quality. Additionally, the machine lifespan is longer than that seen with alternative technologies and there are no internal sealing beads which - among other things - means greater resistance to the high temperatures and pressures typical of pasteurisation processes.