Technologies for the extrusion of recyclable products
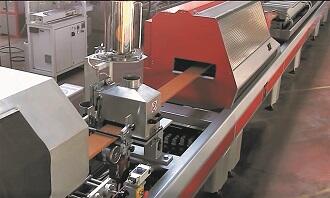
It is undeniable that plastics have become an essential material in the world economy today, but the production of better quality plastic, which is easier to recycle, is essential. In fact, there are two keywords launched by the European Union to reduce pollution: recycle and reuse. Therefore, Friul Filiere puts its know-how at the service of customers to develop new products in line with European directives.
Founded 40 years ago as a producer of dies for the extrusion of plastic materials, the Friuli-based company now sells complete turn-key projects for those who want high quality performance in the production of pipes and profiles. Friul Filiere boasts high-technology extrusion lines, completely customized and guaranteed 100% Made in Italy. Always committed to Research and Development in order to guarantee innovative products to its customers, Friul Filiere feels comfortable facing the sustainability challenges that the market has been proposing for several years. It has manufactured plants for the extrusion of recyclable products and of products obtained by reusing scrap from previous processes as raw materials.
A significant example is the plant for the production of FFC (Foam Fiber Composite) composite profiles: Friul Filiere holds the patent for formulation, equipment, plant, process know-how and characteristics of the extruded profile. FFC is based on a mixture of thermoplastic resins and natural fibres, lightened by closed cell expansion. The true innovative strength of this material is the possibility to recycle and reuse in the formulation not only waste deriving from vegetable fibres (jute, hemp, sugar cane, etc.) but above all scrap from thermosetting plastics classified as special waste (rubber, urea, melamine or phenolic resins, MDF (Medium-Density Fibreboard), paints, etc.). All this leads to sustainable products, representing a significant advantage not only for the environment, but also for the producer, who can take advantage of a reduction in costs related to the supply of raw materials as well as to the disposal of special waste.
Recently, for example, Friul Filiere manufactured several plants that use formulations containing waste from phenolic materials deriving from the production of kitchen doors. Anyone in the world carrying out this activity accumulates tons of waste dust for the disposal of which they must recruit specialized and authorized companies. South American companies that came to know about Friul Filiere’s technology, decided to take the opportunity and reuse these waste to add a series of FFC extruded profiles, in particular floor planks, to their range of products.
Recyclable film for greenhouses
Concerning the commitment to the production of recyclable products, Friul Filiere has been a partner in a project for the agricultural sector. This is a research applied to HDPE film used for the protection of greenhouses, typically characterized by metal eyelets useful for anchoring it to the ground, but making it non-recyclable. The customer required the company to design a completely recyclable cloth. The result was the development and building of an extrusion line for the production of reinforced HDPE film thanks to the HDPE co-extrusion of two side bands and a central band that, punched, replace the aluminium eyelets and allow the finished product to be entirely recycled. This complex plant consists of several in-line units and auxiliary machines, all managed by a single PLC, as Industry 4.0 requires. The result is a flexible system, able to adapt and coextrude the reinforced bands also on sheets of different sizes, suitable for the production of a recyclable product and effective in its application.
Recyclable clip bands
In order to ensure the possibility to recycle the end-product, Friul Filiere has also focused on applications for other sectors. Just think about the technology for the production of the clip bands used in the food industry. Traditionally they are made of plastics and steel filaments, but the latter make the product non-recyclable. To overcome this problem and give an appropriate solution to clip bands manufacturers, that will soon have to comply with the new rigid European recycling legislation, Friul Filiere has developed a solution that provides for the elimination of steel filaments: a coextruded thermoplastic material replaces those filaments, making the extruded product 100% plastic and, therefore, easily recyclable.
The plant includes two extruders (necessary for coextrusion) provided with dedicated equipment. As the sole referent of turn-key projects, as usual, Friul Filiere also supplied the customer with the devices upstream and downstream of the extrusion line, including: the dosing and extruders feeding system, the drying plant, and the end-of-line winding units, collecting the end product.