The other way of moulding rubber
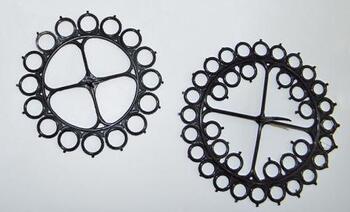
During the recent DKT (Deutsche Kautschuk-Tagung) fair in Nuremberg, Presma exhibited an injection press complete with 12-station mould carousel capable of assuring productivity in line with current market needs, with some interesting advantages over single-mould machines.
Firstly, thanks to the possibility of handling 12 different moulds, assorted production can be achieved using a single injection press, and in the case of the twin-injection unit version, even processing two different blends. Furthermore, in particular in the case of costly blends, the use of small moulds with few cavities, makes it possible to improve the quality of the moulded items and to reduce the scrap generated by flash and sprues.
The vulcanization times, which differ from blend to blend, can be optimized thanks to 10 rotation cycles before the opening and extraction phase of the piece. The press is complete with drive elements that guarantee fast cycles starting from under 5 seconds and injection optimization is assured by a volumetric loading system with hydraulic or electrical drives.
The model exhibited in Nuremberg has been scaled and fitted for two series of moulds with 36 and 16 cavities for O-rings of 10.82 x 1.78 mm and 14 x 1.78 mm respectively. During the exhibition itself it operated without interruption at 5 second per cycle. This machine can be modified in size both in terms of the number of stations and mould dimensions, and therefore in terms of injection capacity.