Cutting PVC pipes without chips and dust
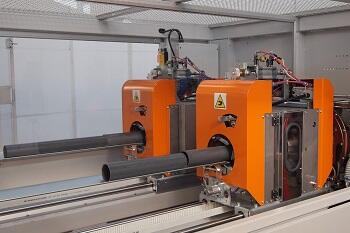
Manufactured by Sica, the Combo 110KW and TRS W pipe cutting machines incorporate a new technology to cut and chamfer plastic pipes without generating chips and dust, resulting in benefits such as raw material savings, lower process management costs, no need for suction systems - given the absence of swarf to collect, store and dispose of - and reduced maintenance (replacement, sharpening etc.) of cutting tools.
The Combo 110KW cutter for PVC pipes from 12 to 100 mm in diameter comes in the 2x1 and 2x2 versions. In particular, in the 2x2 version, it is an automatic machine that integrates 2 haul-off units and 2 cutters in parallel for the feeding and cutting, with blade tools, of extruded rigid pipes in double extrusion, also with different speeds on the 2 axes. Each haul-off unit is configured with two tracks. The upper one is tilting and pneumatically positioned (to adapt suitably also to line start-up conditions), while the lower track is also of variable height but can be mechanically positioned to fit the various diameters being processed. All the caterpillar chains are built with pads in special neutral vulcanized rubber for high friction and low wear, while each of the four tracks is equipped with vector motors and new transmissions to deliver maximum performance with reduced energy consumption.
The cutting system is the planetary type with automatic synchronization of the speed of cutting carriages with the speed of the haul-off units for a superior final quality in terms of precision of the desired length. Each cutting unit is equipped with the innovative W system (Sica patent) where the portion of the pipe to be cut is locally heated by means of IR lamps. The area is then cut by material separation with dedicated tools, therefore it is also possible to cut PVC pipes without generating chips or dust and preventing any deformation on the external diameter within the cutting area. The result is a perfectly straight final surface free from burrs or bulges. The cutting units remain perfectly clean and auxiliary suction and chip collection systems are no longer necessary. Two touch-screen control panels (one for each line) make it possible to manage easily and independently the two extrusion axes while the protection and anti-intrusion systems ensure the safe operation of the machine.
The TRS W model for cutting and chamfering PVC pipes from 25 to 500 mm in diameter is available in the 160 W, 250 W, 400 W and 500 W versions, all of them featuring patented cutting and chamfering methods. These machines are able to chamfer PVC pipes totally swarfless, and thanks to a localized deformation action, it is possible to obtain perfectly formed bevels free from roughness and sharp edges which are notoriously harmful to the integrity of seals during the pipe joining step.
All models incorporate an electrical synchronization system and a double-belt movement for high dynamics and are equipped with “cutting-on-the-fly” feature and a CNC system that ensure the necessary precision of the cut pipe length (± 1 mm). This system guarantees perfect synchronization of the cutting/chamfering unit with the pipe speed and its consequent accurate positioning at the exact point to be cut/chamfered. The “cutting-on-the-fly” feature optimizes the operating stroke of the cutting unit, increasing its potential in terms of cutting/chamfering cycles performed. All models are fitted with touch-screen colour operator panel, with clear and legible icons, and a remote service option for diagnostics and real-time service on the machine.