Gravimetric batch dosing unit for film extrusion
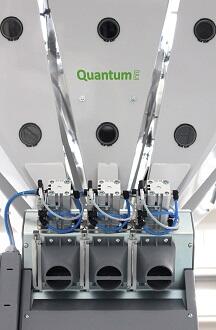
With the Quantum E dosing system, Piovan improves both the effectiveness of the production processes and the product thanks to the high technological content of the new dosing systems, which ensure maximum precision in pellet dosing and total processing control.
The benefits of the Quantum E solution
Quantum E is the new gravimetric batch dosing unit with continuous extrusion control that completes the Quantum series of next-generation dosing units introduced on the market in 2015. With this innovative design, Piovan combines, in a single high precision system, both gravimetric dosage versatility and the accuracy of the continuous loss-in-weight system.
The native control of Quantum E can manage 1 to 8 dosing stations, and the system ensures accurate weighing and complete traceability of each component of the blend. The weighing station and mixing shaft are removable without the need for tools and are fully accessible, as well as the mixer chamber. The load cells are equipped with an integrated automated cleaning system (patent pending) that comes into operation after each cycle. The new design of the discharge system allows the entire hopper to be emptied, leaving no residue; the material is conveyed optimally, without mechanical stress or the risk of crushing the pellets.
Innovation and versatility
Quantum E allows a versatility of use that has never been achieved before, thanks to 8 dosing stations: each station is added or replaced by a simple mechanical operation without the need for complex manoeuvring and in conditions of complete safety for the operator and for nearby equipment.
The gravimetric batch dosing system precisely weighs each of the ingredients of the mixture, while loss-in-weight technology allows total control of the extruded product output and maximum weight continuity per metre of the film.
Quantum E
evolves with respect to similar systems: thanks to the two load cells with
loss-in-weight technology, whereby material consumption is measured
continuously and gravimetrically; in substitution of the slide gate station it
is possible to install an auger station to precisely modulate the micro-dosage
of the ingredients.
Quantum E is the ideal gravimetric dosing system for the production of flexible packing film. For this reason, it integrates technological solutions that offer the best dosage accuracy and maximum precision in weight control per meter of output. Keeping the weight/metre ratio constant is essential in blow film extrusion, as it means: savings in material; optimizing of material use; reducing of waste.
Accuracy, control at every stage, effectiveness
The Quantum E dosing system has been designed and built in such a way as to allow complete traceability of each component and the repeatability of each cycle, also as a consequence of the new trapezoidal shape of the dosing gate, which allows further precision (in dosing), with the integration of a rapid unloading device.
The particular design of the patented spherical mixer, also prepares a completely homogeneous blend of the various ingredients with loss-in-weight control. The mixing action is improved and the hemispherical form of the mixer prevents any pellet stagnation. Quantum E guarantees the consistent quality of the final extrusion in terms of composition and characteristics.
Quantum E can be configured both for single extrusion lines and for coextrusion.
In the coextrusion configuration, the Quantum E dosing and control system adjusts the flow rate of each individual extruder.
Managing each parameter in real time
The use of Quantum E is simple and intuitive: control is achieved through a latest-generation PLC system, while a new HMI allows the operator to view the running of the process and all the operating parameters in real time. Any measurements and adjustments can be made directly and quickly. The Quantum E control, available in 11 languages, guarantees extreme flexibility in customisation.
The advanced control provided by Quantum E was developed by Piovan and acts in accordance with a new algorithm for the calibration of dosing stations. It allows management of a 1-11 layer system and guarantees maximum accuracy of the blend right from the first batch: there is no waste of material, not even during calibration, since the dosing unit ensures that the pellet mix is precisely as desired. It is a control that allows maximum personalization and flexibility, operating through various data exchange standards (Ethernet, Profibus), to configure and use the dosing unit, adapting it to the plant's production needs and the type of extruder.
Quantum E can be controlled remotely through a normal network connection, and is ready for complete integration with Winfactory 4.0 , the new Piovan software release for supervising production processes conceived for the Smart Factory.
Quantum E complies with the latest safety and consumption regulations; for more reliable and simple maintenance, it is equipped with high-efficiency motors that use 30% less energy than previous models.
To satisfy any extrusion application, Quantum E is available in three models - QE200, QE600 and QE1200 - with different initial configurations: for capacity - from 50 to 1200 kg/h - according to the model, all with the ability to natively control up to 8 dosing stations; available with integrated control to manage both the speed of the extruder and the winding speed of the film.