Pandemic and remote commissioning: turning a challenge into an opportunity
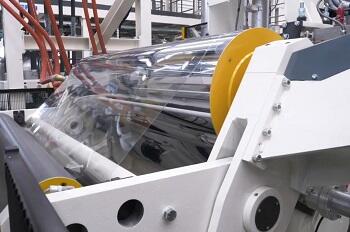
In recent times, a way to limit the spread of the Covid-19 pandemic has consisted of the adoption of behaviours such as social distancing. However, the compliance with these rules, as well as with others indicated by the competent authorities in order to overcome the current health crisis, has not prevented many companies from continuing their activity, even taking advantage of the situation to find new ways of action and collaboration.
That is exactly what happened with Bandera, Siemens and FAE (Siemens partner, and system integrator). In fact, these companies not only managed to deliver, install and start-up a plant for the extrusion of recycled plastic material on time, but they also implemented new methods to do it. Easier, more performing, cheaper, in line with the current orientation of Confindustria’s programme Digital Innovation Hub Lombardia.
The project started because a company headquartered in the UK requested a PET sheet production line for food packaging. With the advent of the Covid-19 pandemic, the start-up of the line at the customer’s premises was put at risk by the severe restrictions to the international movements of the manufacturer’s technicians. The solution soon took shape: a fully-remote commissioning procedure was carried out within the envisaged time frame, even allowing cost reduction.
The remote commissioning was possible because the technology already installed on the plant, under the Siemens brand name, allowed - with some ad-hoc implementations - to manage every phase of the commissioning procedure at a distance. FAE equipped the plant with Siemens technology that, allowing all the equipment (driver, PLC, safety modules etc.) to communicate using a single protocol, ensured the interconnection of all the parts of the system by guaranteeing the highest cyber security standards inside the production area, as well as the integration of the OT with the corporate IT network.
The current technology allows to manage not only the commissioning phases but also those concerning remote monitoring and assistance from a control room dedicated to the remote management of the technical control. During the start-up phase, the technicians checked the complete compliance of the system in relation to the project specifications, intervening in real time in case of correction.
In the pandemic context, the plant commissioning was carried out within the established time frame but, even without considering the movement restrictions imposed by the governments to limit the spread of Covid-19, remote activities on the plant always guarantee at least the following advantages: constant maintenance and predictive controls, immediate intervention, specialized support in real time for the technicians during the installation, economic advantage
It is therefore clear how, in a short- and long-term perspective, remote control technologies applied to the plants become not only preferred, but also necessary.
Considering the commissioning procedure, together with the complete management of the machine, the remote control technology will be increasingly required also during the monitoring and assistance phases. In the first case, in order to correctly check the functioning of the plants and to prevent machine downtime and, in the second one, to carry out maintenance or correction interventions.