Breaking new ground with monitoring system for injection moulding
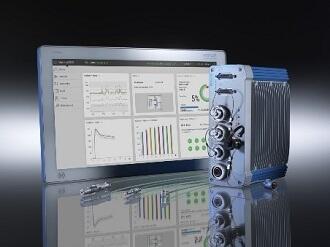
At Fakuma 2018, the Kistler Group showcased its latest monitoring and control packages for ComoNeo, its high-quality process monitoring system that is designed to deliver efficiency and transparency for injection moulding. Unlike ever before, system users can choose their own packages from the vast range of functions available in the system.
ComoNeo is the system of choice for plastics processing companies looking to boost product quality and cost efficiency by optimizing their injection moulding processes. Kistler is constantly developing this process monitoring system - not only to accommodate new application cases but also to ensure comprehensive optimization in every respect coupled with maximum cost efficiency.
Based on the measurement of cavity pressure with tried-and-tested sensors from Kistler, users are provided with modular functions to support predictive control of the injection moulding process leading to optimum results. Support, monitoring, control and prediction make Version 3.0 of Kistler's ComoNeo the leader in process transparency, which is essential for Industry 4.0.
ComoNeo: guiding users to desired results
A key benefit of this system is its ability to support users according to their individual levels of know-how. Kistler has integrated a prediction tool into ComoNeo: the Stasa QC software, which uses measured values and statistical analyses to calculate the quality of the manufactured components in advance, and to assess them within the tolerance bands. This special type of process monitoring is particularly useful for manufacturers of high-grade parts - in medical technology or other sectors where safety is critical, for instance.
To ensure optimal product quality and cost efficiency for their injection moulding processes, customers can tailor their own ComoNeo with these functions:
- ComoNeoPredict: allows model-based prediction of specified part quality based on the cavity pressure and temperature profiles - for optimum process parameters and transparent processes;
- ComoNeoMerge: when multiple components are used, process technology becomes more complex - but ComoNeo 3.0 can easily accommodate this challenge; the system monitors and evaluates up to four components with different mould technologies;
- ComoNeoMultiFlow: for moulds with multiple cavities, this option allows hot runner balancing through individual adjustment of the nozzle temperature - to ensure identical injection conditions in all cavities and automatic correction of deviations;
- ComoNeoSwitch: this function ensures automated switchover from the injection phase to the holding phase at the ideal time - for balanced injection behavior and optimum mould protection during the process;
- ComoNeoComposite, another new feature: injection moulding with the RTM process can now be optimized; special RTM sensors from Kistler create the conditions for controlled high-quality machining of long-fibre composites;
- ComoNeoGuard: this function helps users to define monitoring windows that enable accurate separation of good and bad parts on a step-by-step basis; the benefits: guaranteed part quality and less pseudo scrap;
- ComoNeoRecover: this feature makes it possible to reproduce a proven injection moulding process on a different machine; the user is guided through the adaptation step by step, deviations are identified and the assistant suggests corrective actions.
ComoDataCenter: transparent processes enhance quality and cut costs
As soon as ComoNeo has been specifically tailored to individual application, everything quite literally comes together in the ComoDataCenter, a database that stores all the process data and establishes a seamless communication with overarching systems. Users benefit from the comprehensive overview of their entire injection moulding production, which ultimately provides for a sound basis for ongoing analysis and optimization.
"We're offering companies a complete modular and multifunctional package that fulfils all the requirements for intelligent and efficient injection molding. ComoNeo is Industry 4.0 put into practice”, said Robert Vaculik, head of Kistler's strategic business field plastics. “Mastery of new processes and greater levels of complexity shows the full extent of what injection moulding can achieve in terms of quality - and the potential of process-integrated quality monitoring is far from being exhausted. Development is certainly set to continue".