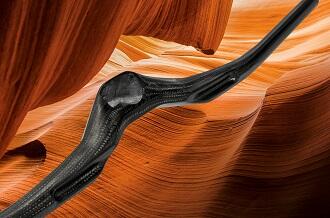
Il vincitore di quest’anno nella categoria RTM del concorso JEC World Innovation Awards ha dimostrato come sia possibile produrre in serie a prezzi competitivi corpi cavi complessi grazie a un processo automatizzato. Il progetto congiunto di KTM Technologies, H2K Minerals, Teufelberger e Basf ha adottato una visione integrata della catena di lavorazione, dalla produzione del nucleo e del preformato con fibre di carbonio intrecciate, passando per il processo HP-RTM (High Pressure Resin Transfer Moulding, stampaggio con trasferimento di resina a pressione elevata) con resina poliuretanica (“processo reattivo”), fino alla dissoluzione del materiale del nucleo. Il progetto, denominato “Cavus”, ha prodotto un corpo cavo geometricamente complesso con incavi posteriori, come un manubrio per mountain bike. Il dimostratore tecnologico ha unito le tecnologie di lavorazione più recenti a materiali maturi in un processo che è sfruttabile per la produzione in serie di parti leggere concorrenziali per il settore automobilistico, ma non solo.
Il progetto è stato avviato da KTM Technologies (filiale
dell’importante produttore di motocicli sportivi, che svolge funzione di
“laboratorio d’idee” per l’intero gruppo KTM), la quale si è assunta il ruolo
di capofila e la responsabilità dello sviluppo dei componenti, nonché della
produzione degli stampi e delle parti. H2K Minerals ha poi sviluppato e
prodotto i materiali per il nucleo, compatibili con il processo HP-RTM. Il
preformato intrecciato è stato sviluppato, ottimizzato e fabbricato dalla
società austriaca Teufelberger, specializzata nello sviluppo e nella produzione
di funi in acciaio, cavi tessili, nastri metallici e parti composite ibride.
Basf ha invece contribuito con la simulazione del processo e il sistema
poliuretanico (PU).
Il punto di partenza per il componente è il nucleo appositamente sviluppato, resistente alla pressione e alla temperatura, costituito da sabbia e additivi idrosolubili, il quale può essere formato in numerose geometrie differenti. La preformatura è stata possibile grazie a un processo d’intrecciatura delle fibre di carbonio completamente automatizzato. Con tale tecnologia si sono potute realizzare geometrie complesse con una portata di materiale elevata. In ragione della perfetta distribuzione, il preformato prodotto assume già il contorno finale del componente finito.
Il successivo processo HP-RTM presenta tempi d’iniezione brevi e un sistema poliuretanico compatto e altamente reattivo, il quale ha ridotto drasticamente il tempo di ciclo a 2-3 minuti. Grazie all’elevata pressione interna dello stampo è stato possibile bagnare interamente le fibre di carbonio per produrre geometrie complesse dei componenti, con un elevato contenuto di fibre. Il poliuretano Basf a indurimento rapido Elastolit R 8819, per parti composite rinforzate con fibra continua, ha evidenziato eccezionali qualità meccaniche, quali, per esempio: un’eccellente capacità di carico permanente, resilienza e tolleranza all’urto elevate. Lo strumento di simulazione Ultrasim di Basf ha contribuito a individuare la gestione ottimale del processo e a ridurre il carico meccanico del nucleo durante l’iniezione.
Al termine del processo, il materiale del nucleo è stato
dissolto in acqua, un metodo che è possibile utilizzare anche con cavità dei
componenti di piccole dimensioni. In funzione del metodo di produzione, è
possibile riutilizzare fino al 98% del materiale del nucleo per la produzione
successiva.