From Itib Machinery the new high-performance FV32/112HP corrugator
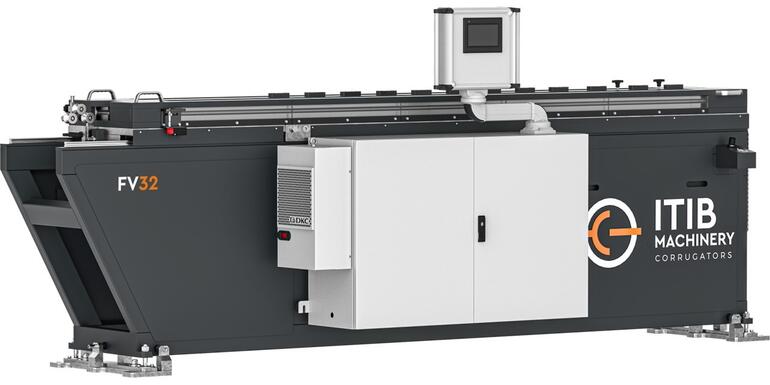
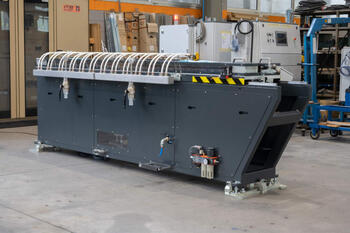
ITIB MACHINERY is delighted to talk about its new high-performance corrugator, the fastest of its range, particularly suited for all the markets who need no compromise, high speed production of small diameter pipes. Its name summarizes all its main features: FV identifies the vacuum forming system, 32 the pipe maximum outer diameter in mm that can be produced, 112 the number of pairs of moulds that make up the chain and, finally, HP is the abbreviation of high performance.
In fact, the main target was to design a corrugator in such a way that it was able to fully exploit the potential of modern extruders and coiling systems, moving any bottleneck in the production line far from the corrugator.
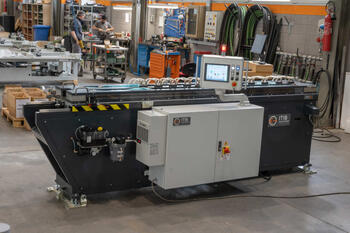
Of course, extreme performance cannot be at the expense of reliability, accessibility, ease of use and quality of the final product.
The attention paid to all these aspects by the technical department of ITIB Machinery emerges clearly in the design and technical solutions adopted in the new, super-fast corrugator.
Technical specs and innovations compared to the previous version
It is clear that the main feature of FV32/112HP (click here) is the high production speed: 80 metres per minute is its maximum mechanical speed; high enough to meet the most demanding requirements, in terms of performance, for the production of PVC, PP and PE conduits.
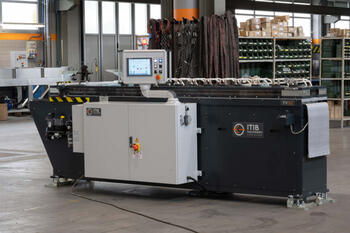
Running a corrugated pipe at extremely high speed is the result of the balance of different conditions: number and dimension of the moulds, cooling efficiency, temperature and flow of the coolant and possibility to manage the thermal expansion of the moulds chain without any risky action of the operator during the production. For this reason, a totally new design characterizes the corrugator: each half moulds chain is moved by separate gears, driven by a single brushless motor with gearbox and torque limiter to avoid damaging of the moulds in case of jam. Additional central free running gears, along with the independently controlled cooling and right/left channels temperature setting prevent chain thermal expansion issues.
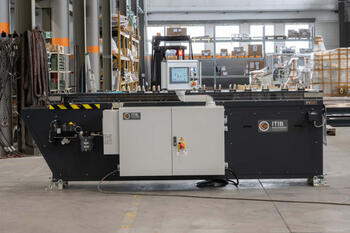
Moreover, the optimized length of the forming channel, which is more than 10% longer with the same total chain length, and the cooling on all four sides of the moulds are essential keys to make the production faster and more efficient, always ensuring a high-quality pipe, guaranteeing a constant and perfect shape during the forming process. An enlarged cross section of the water-cooling channels also participates to the high cooling capacity of FV32/112HP.
Openable inlet covers grant an easy access to the closing channel in case of material jam, thus reducing downtime of the extrusion line. The optimized path of the moulds is confirmed by a smooth hit-free sound of the running moulds at any speed and its design in the closing section allows to obtain a very reduced length of the extrusion die, to decrease the head pressure and allow the extruder to fully exploit the high cooling capacity of the machine. Any top cover of the closing/opening and central channels can be easily and independently removed after fast emptying of the cooling circuit, operable directly from the touch screen simply pressing a button.
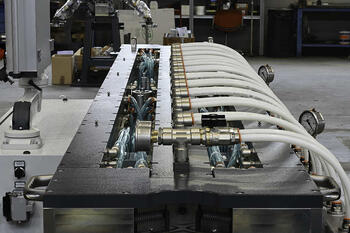
The pushing rack is machined on the rear side of each half mould in such a way that it is possible to remove and replace them easily in any part of the channels; a central pin in the front face guarantees a precise alignment of the two halves and thus a high-quality pipe. The main table is running on high precision linear roller guides and lays on a classic solid tubular frame, which contributes to a vibration free running and allows optimal access to all parts of the cinematic chain, of the water cooling, air, and lubrication circuits.
Despite of the new design and innovations, the new corrugator maintains the same number of moulds of the classic F32/112 and the same mould length as well; the latter solution allows an easier release of the pipe at the outlet channel in case of vacuum forming, compared to solutions with longer blocks. The channels where the moulds are running are faithful to ITIB Machinery tradition as well; in fact, each section is sturdy and made from single solid steel blocks where the “U” or “C” shapes of the channels and high precision long holes are milled and machined. The respect and control of very narrow tolerances thanks to 5 axis CNC machines, where also the moulds are made, are a must to guarantee a safe running at 80m/min.
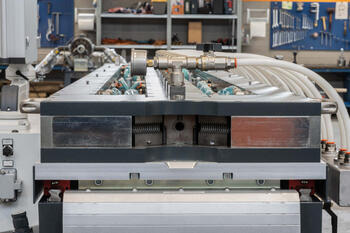
Of course, the HP version is available in the most common pipe forming systems: blow and vacuum forming. Both of them are used for the production of corrugated electrical conduits employed in buildings and constructions, the main pipe application for which the F32/112HP has been designed: the classic blow forming system for PVC conduits, and vacuum forming for PE/PP conduits and pre-wired solutions with a vacuum pump as part of the supply.
If you want to see our FV32/112HP in action, please watch our video presentation of the product (click here).
An additional cooling tank and puller can be also added to increase the production speed even more up to 25% and guarantee a memory free coiling of the pipe.

Onboard control touchscreen
The FV32/112HP cannot do without being industry 4.0 ready: it can be interconnected with other systems and key areas involved in the manufacturing process, letting data collection and decision making easier and more efficient.
The new HMI display allows operators to directly interact with the FV32/112HP: just one touch to start and stop the machine, control any ancillary devices or equipment, change the main operating parameters, and interact with the PLC; the system stores all data and alarms and of course can be synchronized with the extruder and downstreams, in order to control all components of the production chain directly from the same display panel and prevent material jam, pushing the corrugator back by means of an air cylinder, far the extruder, stopping it as well and thus the plastic material flow.
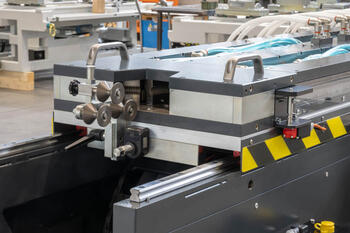
A great attention was given to the solution of major problems connected to extrusion lines for corrugated pipes but to small important details as well; this approach, along with the well-known Italian design catch the attention and make the FV32/112HP corrugator standing out in the extrusion line.
Of course, not only performance, but also safety and energy saving are key points of ITIB Machinery corrugators (click here): the most updated components and ancillary equipments are selected, while consumptions, temperatures and transmission torque are constantly monitored by the onboard control systems.
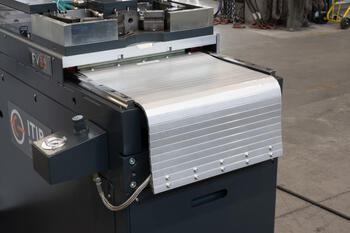
Future projects
Another fundamental piece has been added to the wide range of ITIB Machinery’s corrugators and great interest for its performance and technical solutions is already showed by customers and market. Meanwhile, the company’s R&D activity cannot stop, and new projects are underway to provide ITIB MACHINERY’s customers with equipment that is always up to date with the high expectations of today’s market in any application where corrugated pipes are used. Stay connected to web site www.itib-machinery.com for futher news.
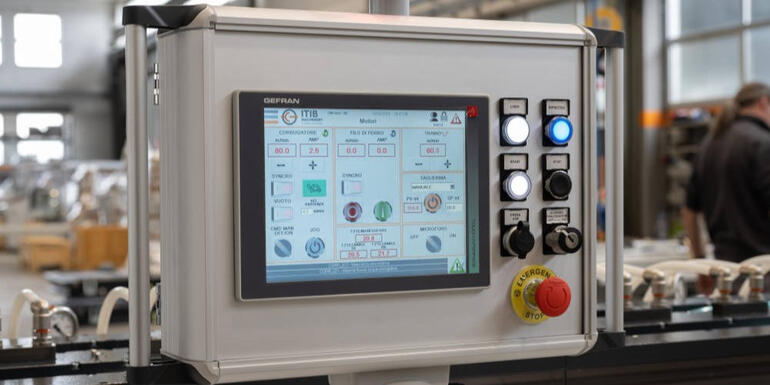