Synthetic paper from twin-screw extruders
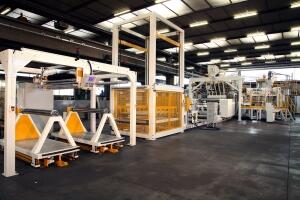
Exploiting its experience in the construction of flat film extrusion plants for industrial applications, such as the production of photovoltaic panels, Union has created a line designed to manufacture synthetic paper, a product which is widely used in Asian countries. The advantages offered by the flat die technology are mainly the low initial investment and the low installation costs.
The line in question can reach an hourly output of 1,500 kg and produce 1,600-kg reels, while the plants currently in operation at the facilities of various Asian processors have an output rate of 2,000 kg/hour (in some cases there already plans to install 5,000 kg/hour lines). Union considers the solution proposed ideal for penetrating the Asian market, which, according to its estimates, could absorb around forty synthetic paper plants at least, leaving aside the fact that the product could also catch on in Europe and America.
The synthetic paper production line is based on special twin-screw extruders developed in-house. Indeed, in synthetic paper, unlike packaging and lamination film, the polymer (polypropylene) content is about 25-30%, while the remaining percentage is made up of vegetable and mineral fillers and additives, which ensure that the product has the appearance and properties similar to those of traditional paper. The extrusion plant must therefore be able to efficiently blend and homogenize the material.
Synthetic paper, thanks to its monolayer structure, excellent printing properties and durability, is mainly used to produce magazines and panels for printing. Unlike traditional paper, it is also resistant to liquids and moisture and does not require the lamination step in order to acquire strength and a shiny finish. Its increased strength also means that is can be processed at high speeds, and can therefore cope with the output rates of modern printing machines, which instead are slowed down by traditional paper. Conversely, a matt finish like that of traditional paper could be obtained by coextrusion, although this is a need that has not yet arisen.