Integrated process for food-grade laminates
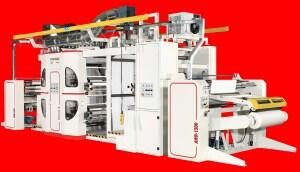
A Superflexol 4-colour flexographic printing machine with integrated lamination and embossing units has recently been installed by Saldoflex at the premises of an Italian processor. A single machine carries out three processing stages (printing, lamination and embossing) to obtain rolls of polyethylene-lined paper ready to be cut to the size required by small and large food retailers.
The food-grade paper coupled with polyethylene - an HDPE film with thickness of approximately 6-8 micron - is commonly used by supermarkets for counter products, butchers, fish markets, delicatessens and so on, for wrapping fresh food products with high moisture content and/or containing oil or grease. The advantage of lamination consists in a far easier recycling process, beginning with separate household waste collection, as the polyethylene film, coupled to paper by means of a cold process, can be easily peeled off and separated from the paper by the consumer after use. All this would be impossible for coated paper, obtained by extrusion coating and hot lamination. The paper also has a clear advantage over wax paper when it comes to recycling.
The lamination and embossing units, integrated into the machine's structure, are positioned after the drying bridge and immediately before the rewinder. The unwinder of the HDPE film is motorized, with electronic tension control. The lamination unit, conceptually similar to a colour unit, deposits a very thin layer of vinyl solution onto the paper just before being pressed on by two cylinders. The dosing of the vinyl solution is done by means of a full-length rubber-coated cliché cylinder, which receives the solution from an engraved copper-coated anilox cylinder. The solution reaches the anilox cylinder from a tank by means of a rubber-coated cylinder, which then transfers it onto the engraved cylinder.
The embossing stage, also a cold process, is carried out subsequently between an embossed cylinder and a rubber-coated cylinder The operator has full control of all parameters: he can adjust the tension of the HDPE film (very important to ensure the paper flatness once it is cut into sheets), its alignment in respect of the paper, the quantity of glue being transferred onto the paper (by adjusting the micrometrical pressure of the anilox cylinder), and the pressure of the embossing cylinder.
The printing section was engineered keeping in mind the speed, flexibility and quality requirements of the processor. Capable of an effective printing speed over 220 m/min, using water-based inks on a width of 1,000 mm, this flexographic press is equipped with cliché sleeves with quick change-out system directly in the machine, to switch processes with short set-up times. It also has a number of motorized simultaneous feeding motions and a video camera to control the register, in addition to a number of features (such as electric hoists for handling the cylinders and hydraulic lifting system for the reels on the unwinding and rewinding units) aimed at easy use - and therefore safe running - of the machine.