Milacron technologies at K 2016 in two booths
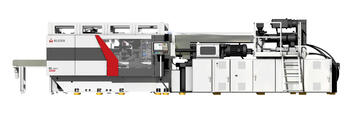
Milacron, a leading industrial technology company serving the plastics processing industry, announces additional key technologies for K 2016. First, the company is displaying its Advanced Plastics Processing Technologies (APPT) featuring Milacron, Ferromatik and Uniloy product branded injection, PET, blow and extrusion offerings in hall 15, booth C06. Milacron’s Melt Delivery and Control Systems (MDCS) is in hall 1, booth A39, featuring product brands Mold-Masters, DME, Tirad and Cimcool.
“We’re excited to provide an additional glimpse of what you can expect to see from our company at K 2016. Milacron is one of the few integrated plastics processing provider”, said Tom Goeke, CEO of the holding. “Our customers have come to rely on Milacron for the finest quality products, leading technological advances and unprecedented customer service, all of this is on display in our two impressive booths”.
PET preform system with co-injection barrier technology
Milacron marks its European show debut at K 2016 with its co-injection PET technology M-PET 300. It consists of a servo-hydraulic co-injection PET system, which combines key components across Milacron’s product portfolio - machines, clamps, injection unit, post mould cooling, co-injection hot runner, mould and robots - into a single solution. The M-PET system is utilizing a state of the art co-injection hot runner system and co-injection nozzles featuring Kortec technologies. Co-injection allows the simultaneous injection of two materials in the same mould cavity to produce a barrier solution.
Steve Morris, president of Milacron Systems stated: “Our established, German designed, Ferromatik-Series machine platform provides our customers with a reliable injection moulding platform that introduces speed and efficiency to our co-injection hot runner technology. Our customers continue to provide us with positive feedback and note that Milacron’s PET systems are amongst the quietest, easily maintained, and very impressive regarding low energy consumption based on the electrification of the system. Another key feature is the low cost to run a Milacron PET system. Aside from low energy, our systems utilize standard technology reducing the number of special higher cost parts (no servo valves are used) which also ensures parts availability”.
The system is designed to co-inject a bottle grade PET skin with an oxygen barrier core. The combination of these materials provide the mechanical properties and clarity needed for a PET container with an oxygen barrier to extend shelf life. Due to the simultaneous injection of both materials, there is no fill time penalty and the system is capable of running at monolayer cycle times.
Even faster colour change in closures injection moulding
Milacron’s Mold-Masters hot runner product brand announced that their industry leading closure hot runner, Sprint has launched new colour change tips. The new tips are engineered to far exceed the performance of similar competitive systems. The new Sprint colour change tip improves colour change by up to 47% (vs. a standard gate tip). These new gating tips are available immediately as a standard package for all Sprint systems and are compatible with the current tip as replacements. Mold-Masters Sprint closure hot runners are engineered for speed. Sprint is available in hot and valve gate solutions engineered for lightning-fast cycles, colour changes, optimal part quality and greater durability for maximum uptime, while dramatically reducing overhead.
New six servo axis controller
The new Mold-Masters M-AX servo axis controller is Milacron’s most technologically advanced controller to date. It has the same powerhouse TempMaster Adaptive Process System (APS) used to control temperature in its entire temperature control line up but also contains an unmatched ability to control motion functions as well. Servo control functions include valve stems, core pulls, coining plates, index plates, stripper plates, ejector plates as well as driving Mold-Masters technologies like E-Drive syncro plates and Single electric Valve Gates (SeVG). This brand new technology is on display in the MDCS booth A39, hall 1, featuring a fully functional multi-axis mould provided by Accede Mold. Mould base and components are from DME.
A truly “smart” cell for injection moulding
The SmartMold module is the result of a multi-year development to make injection moulding machine cells truly “smart”. It allows different pieces of equipment to talk to each other, impro
ving process quality and efficiency all while providing improved information and metrics. SmartMold collects data and reports the data via the cloud or LAN. It also allows for the scheduling of regular and preventive maintenance. SmartMold is featured on Milacron’s MPET 300 machine producing PET preforms with co-injected barr
ier layer, the Mold-Masters Summit valve gate display system and the new M-AX six servo axis controller system.
A customer contest to celebrate the new eStore
Milacron’s new eStore, launched in July, has received overwhelmingly positive feedback while processing thousands of customer orders in North America and Europe. The Milacron eStore team is holding an exciting sign-up contest live in both Milacron booths. Qualified entrants are walked through the new customer sign-up process and in doing so are entered into the daily draws. Prizes include iPads, iPods and much more. The Milacron eStore is offered in 15 languages. The mobile friendly, e-commerce site is seamlessly integrated with the newly re-designed website (www.milacron.com), offering a one-stop-shop for all Milacron products, including individual parts and assemblies. Cus
tomers also have access to DME’s vast catalog, connecting them to an unrivalled selection of mould components and MRO supplies 24/7/365. Customers benefit from simple, cost-efficient ordering, shipping and deliveries within 24-48 hours.