Innovative materials and computer simulation for optimized shanks for shoes
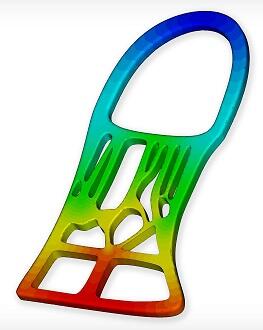
From February 20-22, 2019, Simac, the international machinery and technology exhibition for shoes, is being held in Milan and Basf is presenting the newest material developments together with Ultrasim computer simulation, targeted specifically on manufacturing optimized shanks for shoes.
Material and process innovations for shanks
A shank is a stiffening element between the inner sole and outer sole of a shoe that retains the shoe’s shape and makes the shoe more comfortable to wear. Stiffness is the primary property required by the shank material, which is why it is often made from a glass fiber-reinforced polyamide or other materials.
The team of experts at Basf developed a new solution for shanks through use of a glass fibre-reinforced thermoplastic polyurethane (TPU): The new Elastollan R series from Basf exhibits the stiffness of alternative materials and absorbs hardly any moisture. Benefits: it adheres very well to PUR while a time-consuming and costly surface treatment is no longer needed. But there is more to it than that - this is where Ultrasim comes in.
More design, less material and lower costs
Ultrasim, the comprehensive and flexible CAE competence of Basf, has now been employed for the first time in the shoe industry. Using Ultrasim simulation technology, it is possible to design highly stressed lightweight parts efficiently with the goal of meeting specific requirements. In this way, Basf was able to manufacture a lighter TPU shank. The greatest benefit of this Basf service is reaped by customers who use closed shanks with surface optimization. At the exhibition booth, Basf experts will evaluate jointly with customers in which special customer projects such simulation can be employed meaningfully.
A valuable cooperation
Manufacturing sustainable shoe components is a goal to which the Spanish company Analco is committed. Having sustainable materials for sole production in its portfolio – one of the benefits from Basf. The years-long partnership between Basf and Analco also bore fruit for the latest initiative: with its Elastopan Green (PUR) and Elastollan N (TPU), Basf was able to offer products manufactured from up to 50 % bio-based renewable raw materials - certified by Astm D 6866-12. At the same time, it should be noted that these are not obtained from agricultural products, and thus do not reduce acreage used for food production. In addition, both products offer exceptional mechanical properties such as abrasion resistance, design freedom in the case of TPU, lightness and comfort in PUR, matching those of comparable standard products. The results of this initiative speak for themselves and fulfill customers’ needs for sustainable products: Both Analco and Basf present the results at their exhibition booths.