Heat-resistant PA for the turbocharging in the 2017 Alfa Romeo Giulia
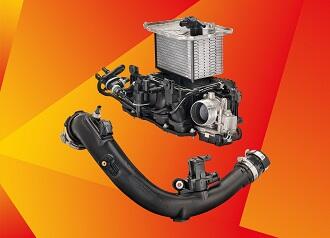
Basf is introducing its heat-resistant polyamide Ultramid Endure in two new powertrain applications on the 2017 Alfa Romeo Giulia: the air intake manifold with integrated charge air cooler and the hot-side turbo duct. As heat under the hood increases, Ultramid Endure with its high heat-aging resistance up to 220°C enables automakers to achieve engine downsizing and turbocharging without sacrificing performance. The Ultramid Endure grades offer good processability, excellent weld line strength and are available globally.
Basf collaborated with the automotive supplier ABC Group, Canada, to develop the hot-side turbo duct for the Alfa Romeo Giulia. For this application, ABC Group decided on Basf’s Ultramid Endure D5G3 BM, a 15 percent glass fibre reinforced blow moulding grade, which has a high hose strength and shows good swelling.
ABC Group leveraged Basf’s joining technology expertise to optimize the infrared (IR) welding parameters for this part. It was crucial to achieve strong weld lines to ensure the long-term durability of the duct. “After conducting numerous resin trials through moulding, welding and rigorous validation testing, we were able to meet the significant demands on this application,” said Mary Anne Bueschkens, CEO of ABC Group. “The part requires many weld connections. Our engineers worked closely with Basf’s material and joining experts to understand the unique requirements, allowing us to fine-tune our IR welding technology, and assuring success of the welding process for this demanding high-temperature duct”.
Basf worked with Magneti Marelli, a business of Fiat Chrysler Automobiles (FCA), to develop the air intake manifold with integrated charge air cooler for the Alfa Romeo Giulia. The need for a material to withstand a 200°C continuous use temperature made this air intake manifold a prime candidate for Ultramid Endure D3G7, a 35 percent glass fibre injection moulding grade. The air intake manifold also required an excellent burst pressure performance; therefore, Magneti Marelli needed a material that offered reliable weld strength at elevated temperatures.
With Basf’s design, material and processing expertise, Magneti Marelli could achieve the required burst strength and durability for the assembly. “BASF’s technical support was useful for us to ensure the application met the burst requirements,” said Marcello Colli, product manager Throttle Bodies at Magneti Marelli. “Basf’s welding experience enabled us to apply this heat-resistant material and meet long-term durability targets.”
The Ultramid Endure grades are suitable for many powertrain applications of the turbocharged system including air intake manifolds, charge-air ducts, resonators, intercooler end caps and throttle bodies. They can achieve long-term service temperatures of 220°C, and withstand peak temperatures of 240°C. The notable heat aging behaviour results from an innovative stabilization system by BASF, which greatly reduces oxygen attack on the polymer surface.