The combination between conference and exhibition
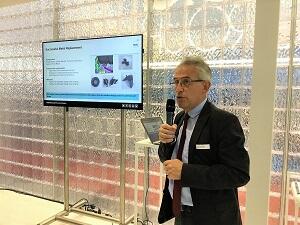
On May 12, at Villa Ottoboni Congress Centre in Padua (Italy), RadiciGroup Performance Plastics and its partners held a one-day customer-centred event featuring presentations, discussions and exchanges of ideas on products and innovation. This RadiciDay, attended by about 100 people, was the latest in a series of initiatives organised by RadiciGroup, which has always kept customers at the centre of its development work.
Numerous topics were raised by RadiciGroup Performance Plastics in the course of the event: from the re-organisation of its sales network in the Veneto and Emilia Romagna areas to its product range, latest innovations, and the structure and benefits of its CAE service offering computer-aided customised technical support. Among the attendees were Angelo Radici, president of RadiciGroup; RadiciGroup Performance Plastics management; Fidel Garcìa-Guzman, chief executive officer of Guzman Global; and Goffredo Berardini, chief executive officer of Bilco.
“This RadiciDay was an important opportunity for us to dialogue with our partners”, said Enrico Facciolo, sales manager for Italy and the Iberian Peninsula of RadiciGroup Performance Plastics. “The event created the right atmosphere, allowing us to meet face-to-face and build relationships, which is what distinguishes our customer approach”.
“Being closer to our customers is the precise objective of our new sales network structure in the Veneto and Emilia Romagna areas”, Facciolo continued. “And the appointment of Elisabetta Tarquini as our area sales manager is a further sign of our presence in the territory. Having a sole distributor with the capability of improving the offering of available inventory, together with a unified vision of the target market, means providing retail customers with a firm point of reference, which will serve as a go-between to pass on their needs to us, the manufacturer. In practice, there will be a team dedicated to the needs of our present customers, as well as potential ones”.
Starting on 1 January 2016, Bilco, part of the Guzman Group, is appointed as the sole distributor of the entire RadiciGroup Performance Plastics product range (Radilon, Radistrong, Radiflam, Heramid, Raditer, Heraflex and Heraform) for the Veneto and Emilia Romagna areas. The morning session opened with a welcome by Cesare Clausi, global sales manager of RadiciGroup Performance Plastics, and continued with talks by (in order of appearance): Enrico Facciolo, who presented the new sales network organization; Fidel Garcìa-Guzman and Goffredo Berardini, who explained the Guzman Global Group; and Andrea Panelli, of RadiciGroup Performance Plastics Marketing and Technical Assistance, who focused on the RadiciGroup product portfolio.
The afternoon session opened with Angelo Radici, president of RadiciGroup, who gave an address thanking employees, collaborators and customers, and continued with Erico Spini, marketing and application development director for Europe of RadiciGroup Performance Plastics, and Carlo Grassini, of RadiciGroup Performance Plastics Marketing and Technical Assistance, who spoke on innovation and the CAE service.
Inno Pro Wire at RadiciDay
“RadiciDay is a time tested type of event based on the fact that, under certain circumstances, supply and demand will benefit from meeting in a neutral and pleasant location, where both parties are a little freer from interferences such as may come from daily company duties”, explained Cesare Clausi, global sales manager of RadiciGroup Performance Plastics, during a break in the May 12 meeting that gathered together in the stupendous sixteenth century Villa Ottoboni few kilometres from Padua’s city centre, Clausi’s team with a good ninety buyers and technologists from Veneto and Emilia Romagna dealing in automotive, home appliances, home furnishings and electronics.
RadiciDay is about strengthening relationships with our customers, forming new ones and sharing/debating technical issues related to polyamides and strategic/managerial issues face to face.
Cesare Clausi introduced a second piece of news: “There is another message that we are conveying at this RadiciDay, which is about the current greater range completeness of our polyamides - PA 6 and 6.6 in particular, but not only - achieved thanks to the significant investments we made in new manufacturing processes at our plants”.
Another message conveyed during the meeting dealt with the great “attention paid to the demand coming from the market”, which can happen - again according to RadiciGroup - by developing and manufacturing high performance customised products that can meet the customers’ boldest expectations, maybe including organic content and always while complying with current certifications and standards.
With this in mind, Cesare Clausi mentioned a significant example with regard to the project Life+Inno.Pro.Wire (LIFE13/ENV/IT/000614), funded by the European Union through the Life+ programme; a project that Gruppo Industriale Maccaferri (Officine Maccaferri and Samp) is developing in partnership with RadiciGroup. For the record, Officine Maccaferri is a global company, doing business in over 100 countries and with close to 3000 employees trained in the research, design and development of complex technical solutions in the field of civil engineering and geotechnics, with environmentally sustainable projects.
“In 1893, Officine Maccaferri invented, designed and manufactured the so named “gabions” for gravity support works, used in general for land preservation works, radically changing the course of civil and environmental engineering history”, explained Mr Clausi, who went on to say that, “Officine Maccaferri professionals are still innovating everywhere, sharing their knowledge to increase return on investment by customers and partners. Following a European project regarding the use of polyamides as a viable alternative to PVC – for the first time - as a coating for wires that make up metal net protect strustures, the RadiciGroup Performance Plastics business area was chosen as a partner to develop, make and supply a technopolymer custom developed for this application. The final goal is twofold: considerably reduce the environmental impact of the manufacturing process and increase the lifespan of the gabions by several decades!”.