Agricultural applications to benefit from the expansion of Basf plastic additives in Pontecchio Marconi
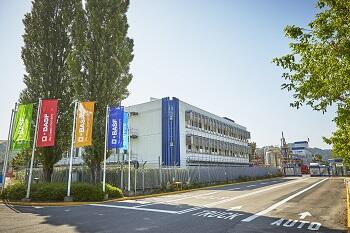
Basf announced the technical completion of the newly constructed plant for the plastic additives business at its site located in Pontecchio Marconi (Bologna, Italy). The state-of-the-art facility will deliver a wider range of NOR solutions to support Basf’s leading position in the strategically important and growing agriculture industry.
The use of plastic materials in agricultural applications, plays an important role in helping farmers enhance crop productivity and food quality in an increasingly difficult environment. Agricultural plastics must be capable of protecting the crops enduring exposure to harsher ultraviolet and heat radiation and be impervious to the chemicals used by farmers to treat plants’ diseases and for disinfection practices. The demand for such reinforced plastics continues to increase rapidly. The novel Basf NOR technology platform consists of a range of outstanding light and thermal stabilizers that are especially effective in plasticulture applications such as greenhouse covers, macro and small tunnels, nettings and substrate bags.
The Basf Pontecchio site has already been a major production unit for hindered amine light stabilizers Hals and NOR Hals product ranges. It is also home to the global testing hub for agricultural applications and the regional weathering center. The expansion makes use of the existing infrastructure and generates new opportunities to serve the growing customer demand.
The new plant, which is equipped with a recently developed digital technology platform, will provide innovative solutions that accelerate the site's progression towards industry 4.0. The new communication platform, for example, allows maintenance, troubleshooting and configuration of instruments to be done remotely over industrial ethernet which provides more security and stability. The design of the plant also incorporates the latest technology to increase energy efficiency, while decreasing CO2 and noise emissions.
The production line includes motors with the highest International Energy efficiency class IE4. The building walls are also insulated with sound absorption panels that reduces the noise emission compared to industry standard. Thanks to these state-of-the-art technologies, the new plant contributes to the company’s sustainability targets.