Black, White & Blue
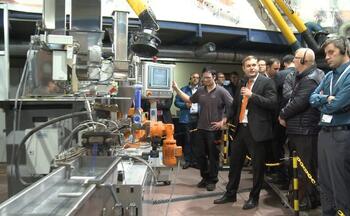
This was the theme of the international Masterbatch Workshop organized by German extruder manufacturer Leistritz Extrusionstechnik on November 17-18, 2015. The event, held for the twelfth time, offered amongst other things an insight into the world of black, white and blue masterbatches for over 100 participants coming from a wide variety of countries. “Our workshop has been an integral part of the plastics processing industry’s calendar for quite some time. You can tell by the high number of visitors who come every year. We combine a unique knowledge transfer by high-quality expert lectures with live demonstrations on our ZSE MAXX extruders in our lab. This mixture of exciting topics in combination with the theoretical and practical parts have al-ways been well received”, said Anton Fürst, managing director at Leistritz Extrusiontechnk.
The expert presentations mainly covered the topics of black and white. Arien de Wild from Cabot Switzerland, a global specialty chemicals company, explained the role of carbon black in relation to three plastics compounds functionalities (color, UV protection and conductivity) and emphasized the importance of adequate dispersion. Speaking of dispersion, Kathrin Lehmann from Evonik also underlined that dispersants are important ingredients in masterbatch manufacturing for high impact polystyrene, polyolefins and even engineering resins.
In addition to Arcadi Prieto, from the Spanish calcium carbonate producer Reverté, and Daniel Lladó from Nubiola, a global producer of inorganic pigments, who spoke of the “cool” pigment ultramarine blue, Willem de Vos, CEO of the Society of Plastics Engineers, also delivered a lecture. What are the mega trends in plastics industry? Where does the journey lead to? He tried to give answers to these questions by means of various forecasts.
The Leistritz experts also gave an extensive insight into the topics the design and processing technology departments are working on. Frank Rechter, head of design department at Leistritz, discussed what possible machine equipment can facilitate a more efficient extrusion process. Process engineer Sebastian Schraube took the audience into the world of nucleating masterbatches and showed what their influence is on processing and material characteristics of e.g. foamed thermoplastics. His colleague Johannes Krückel presented in his paper on conductive compounds which polymers, fillers and extruder parameters one needs to produce them. He demonstrated it with the example of carbon nanotubes. The topic of “ultra-high molecular weight polyethylene” (UHMWPE) was covered by Thomas Unger. For the first time, he ran the process on twin screws, which so far has only been handled by compression molding and rammextrusion. The promising interim result of the test runs show that UHMWPE can be processed on a twin screw extruder in a stable manner by adding only a small amount of additives.
“This year we covered a wide range of topics, so that there was something for every taste. The highlight was definitely the visit to our lab where we subjected three papers to practical testing”, summarizes Anton Fürst. At the live demonstrations 40% of the pigment ultramarine blue was incorporated via split feed and afterwards premix into LDPE on a ZSE 27 MAXX extruder and then compared. The incorporation of 25% carbon black into polybutylenterephtalate was demonstrated on a ZSE 40 MAXX. 80% calcium carbonate was incorporated via two side feeders into LDPE on the ZSE 50 MAXX with an underwater pelletizer.