The revolution in packaging is the ALLWrapper
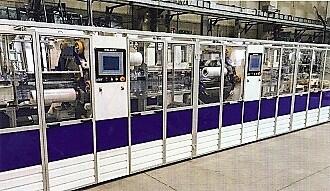
ALLWrapper is the new revolutionary packaging system engineered by Colines. lt uses stretch film as a substrate to perform bundle-wrapping on a huge number of different products. Being manufactured and optimized for the beverage industry, its range of application has been extended to the food, cosmetic and pharmaceutical industries with different machines. The system can handle the packaging of bottles, cans, pots or bags made of different materials such as plastic, carton, metal and glass.
Whilst for some applications the unnecessary use of a shrink tunnel comes as the only cost effective solution to secure products in bundles, as in the case of water bottles, in some other areas the heat generated to let the conventional film shrink around products represents a risky process, above all in the case of combustible materials, or even does not permit to use plastic as protective and logistic envelope, for example in the use of carton packaging for drugs. Similarly to what happened in the evolution on pallet protection, from shrink film to cost-effective stretch film, product-bundling by means of stretch film provides an attractive solution to start saving on electricity and packaging costs.
The ALLWrapper packaging system is covered by several patents and has been engineered on the basis of a modular concept. There are two basic machines that differentiate from each other by their individual operation mode. Whilst the ALLWrapper Basic runs by cycle (the products are bundled at each cycle), the ALLWrapper Auto wraps rows of products in a continuous envelope that is separated in bundles at the end of the process. Regardless of the machine used or the product the be bundled, the mechanical characteristics granted by the stretch film along with the intrinsically money-saving wrapping process (avoiding shrink tunnel), permit an outcome of more than 50% saving on packaging material and more than 90% saving on energy consumption.
“We at Colines are very proud of sharing this cost-efficient and sustainable solution with our customers as a future challenge to reducing the use of resources down to a minimum, no matter if plastics or energy”, say the company’s management.
In the development of the new system, Colines took advantage of the cooperation with ExxonMobil as the provider of the materials for the high-tenacity three-layer stretch film for packaging applications. This film, with a thickness of 10 micron, features an A-B-C structure where the A layer is made of 100% Exceed 3518 mPE material, the B layer of 100% Enable 2010 mPE and the C layer of 95% Exceed 3518 and 5% Vistamaxx 6102 mPP. This formula is intended for ensuring excellent tenacity and tightness even on the thinnest films: Exceed brings tenacity, strength, impact resistance, good optical properties and thickness; Enable combines high processability with HAO (Higher Alfa Olefin) performance; lastly, Vistamaxx ensures high performance and low formulation and process costs.