Integrated functions to reduce the number of installed devices
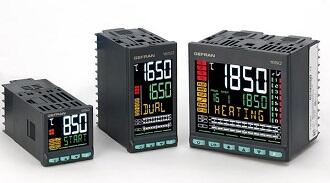
Gefran launches the new Performance family of PID controllers including three models: 850, 1650, and 1850. Numerous integrated functions reduce the number of devices installed on a machine and simplify configuration. Accurate regulation, numerous options and exclusive functions make these devices so intelligent that the system regulating and controlling a production process can be simplified, installing one single device instead of several (double controller, PLC and HMI, timer).
This means the perfect word to describe the new range is cost-effective, as it delivers significantly lower purchase, installation and operating costs with high precision, stable measurement and PID control combined with logical and mathematical functions.
These features make the Performance series the ideal solution for regulated processes such as heat treatment of metals, laboratory equipment, and pharmaceutical and medical sterilisation processes requiring particularly precise, accurate measurement.
The new controllers continue the process of expanding the range and represent the natural evolution of the 650/1250/1350 family, which Frost & Sullivan named PID controller of the year in its category last year. The 850/ 1650/ 1850 series, available in three sizes (1/16, 1/8 and 1/4 DIN), shares many of the exclusive features for which the 650/1250/1350 family was selected for the prize, and offers even more.
A series of features remain unaltered, such as the customisable display, bright lighting and high resolution for easy reading by the operator, easy configuration with a software tool, multilingual messages, functions for planning preventive maintenance and constant monitoring of energy consumption.
In addition, the new series offers numerous integrated functions permitting reduction of the number of devices installed on a machine, simplifying configuration and therefore saving time and money:
- double loop: two independent regulation loops to replace two regulators with one and save on wiring and structural work;
- 32 integrated timers: a single regulator in place of a timer + controller;
- 32 logical blocks, 8 mathematical blocks and additional I/Os: there is no need of a PLC to perform simple control functions such as checking authorisations, machine start/stop commands and alarms, counting pieces produced, making comparisons, etc. And there is no need for an experienced programmer or for complex programming software; the free configuration tool is sufficient.
All options are available on all sizes, starting with 3 additional digital inputs in the smallest size and going up to expansions of 8 digital IN / OUT and 8 R relay outputs in the 1/4 DIN size. These additional I/Os can be managed by logical blocks and permit complete control of a machine with up to 31 I/Os.
Double loop for PID control of two independent zones, cascade control and report control. In casting and maintenance kilns, for example, cascade control provides stable regulation of the temperature of the casting material of the crucible and prevents reaching temperatures that are critical for the heating resistances, thus extending their life cycles.
If, on the other hand, one quantity must be regulated on the basis of another, maintaining a constant ratio between the two (for example, when mixing two fluids), the solution is ratio control.
In addition to PID control, the new Performance family offers a double set point profile programmer. Synchronous and asynchronous profiles may be generated to manage two different temperature zones or for applications regulating two different quantities (temperature and pressure, temperature and humidity), such as incubators and climate chambers in which temperature and relative humidity are programmed with independent setpoint profiles, and synchronised in time with common start, stop and reset commands. Each step may be described with customised scrolling text messages.
Lastly, motor-driven valves are managed with open/close commands and allow position to be monitored and controlled through feedback.