Blow moulding for yogurt containers
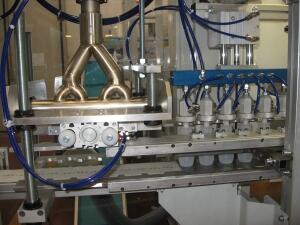
The new HL 350/D dual station fully electric continuous extrusion blow moulding machine has been developed by Meccanoplastica to produce containers with a capacity of up to 3 litres. This model has a clamping force of up to 6 tons and is available with horizontal motion of the mould carriage on 350- or 400-mm parallel prismatic guides.
The mould opening and closing movements, the sliding motion of the mould carriage, the upward/downward movements of the blowing nozzles, and the adjustment of the parison thickness are all driven by brushless motors. The absence of a hydraulic control unit results in elimination of all possible contaminants, silent running and lower energy requirement. It is actually already some time since this manufacturer introduced an electric motor to drive the extruder (the most critical component in terms of power consumption) and the "bobbing" movement (the upward/downward movement of the platform bearing the extruder and extruder head).
In this machine, however, particular attention has been paid to the mould opening and closing motions, which is where the main problems with fully electric extrusion blow moulding machines have emerged. Indeed, in the absence of hydraulic technology, it is not easy to develop consistent and precise clamping force, especially when needing to operate at high power levels in order to produce large capacity containers, perhaps with an integrated handle. The unusual feature of this machine is the hydrostatic-pneumatic system adopted for the mould closing step, as it is driven by a brushless electric motor capable of delivering and maintaining the power required thanks to a booster, yet without using a hydraulic pump.
In detail, the plant has been configured to produce 100-ml yoghurt pots, each weighing 14 g, by a processor who has purchased two machines. The blow moulding machine is equipped with an extruder with a diameter of 90 mm, an electric motor and inverter, a six-parison accumulator head (centre distance 60 mm), and two 6-cavity moulds.
An indispensable requirement for this application, given that it will be used in the food industry, was to prepare containers that are, as far as possible, contaminant free, without the need for a clean room. To this end, in addition to the technological solutions already described, the end of the pot, after blowing, is re-heated and welded, to prevent the penetration of dust and other contaminants and to prepare it for storage and transportation. In the testing phase, the machine reached a production rate of 6500 pots/hour.