Polyurethane ring for oil and gas pipeline
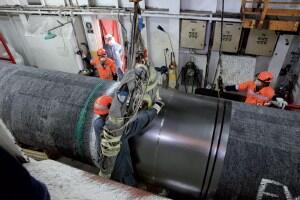
An exclusive program which includes side by side support, tailor-made state-of-the-art technology, personalized technical training and 24 h assistance is offered by Saip to the main players in the oil & gas field. The company has been active in this market for over 15 years supplying solutions characterized by high reliability and fast maintenance, also thanks to the remote assistance.
One of the main applications in this field of the Saip technology consists in the application of a polymer layer on the joints between the different segments which make up a pipeline for gas or oil. This extremely critical operation is carried out before laying line. A sort of polyurethane ring is placed next to the welding of the joints. Thanks to its properties, it safeguards the welding, protecting this later from external agents and ensuring resistance to water pressure, corrosion, salinity, algae etc.
This kind of intervention often takes place in very difficult environments, like sea bottoms, deserts, expanses of ice, which need specific treatments. Generally the treatment is carried out on pipelines made up by steel pipes coated with polyethylene or concrete, having a diameter ranging from 16 inches, for compact materials (elastomeric materials), to 48 inches, for expanded materials, and a length from a few to thousands of kilometers.
Systems for these applications are designed and made according to specific requirements, to operate, for instance, on board of ships, where spaces are very limited and environmental conditions are very severe. Consequently, Saip has been choosen from the main players in this field, such as Saipem, as official partner able to help them in the direct management of such specific and delicate phase. All this required the ex novo designing and engineering of the plants according to specific needs of usage and the training and the support of the onsite personnel to transfer competences to operate in complete autonomy, exploiting at the best the technology potentials.
Thanks to this approach, three Saip systems have worked in the Nord Stream Project for over two years in very difficult conditions, ensuring a perfect welding between the segments of the 1,224-km gas pipeline which connects Russia and Germany through the Baltic Sea bottom.